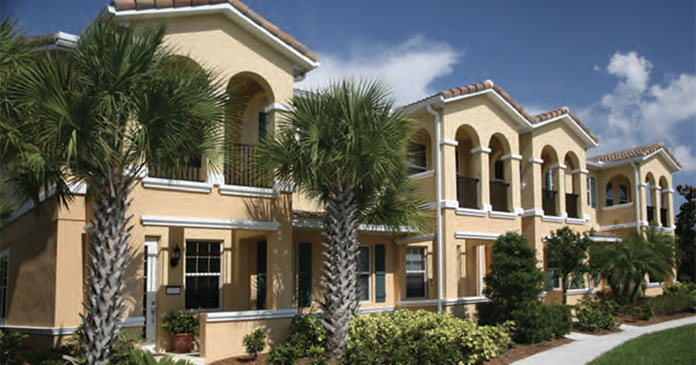
First, an energy and water consumption assessment was commisioned. Simcoe Consulting was designated.
The County of San Diego had just raised the drought warning to a level two for the City of San Diego, and the local water provider, Padre Dam Water District, had steadily raised water and sewer rates in recent years. The property owner, a private company based in San Diego, Calif., were concerned that increasing rates, and potential fines and levies on water use might threaten already slim operational margins. The company owns north of 35 multifamily properties throughout Southern California.
Simcoe set out to address key points: How to maximize the property’s energy-efficiency. What would a green retrofit cost? What was the projected ROI? Were rebate funds available to offset the project cost?
The entire project, from audit to strategy to final completion, took 75 days.
Lay of the land
Santee Villas, built in 1984 on 18 acres in the San Diego submarket of Santee, spans 16 buildings.Northeast of the city of San Diego, Santee has a generally temperate climate, although summer day temperatures often exceed 100 degrees. Logically, and depending on exposure, some buildings get a great deal of sun, and others, very little.
All of the buildings are two-story, wood and stucco construction. The property’s systems (plumbing, irrigation, electrical, HVAC) were installed during the original construction. No major retrofits or upgrades had been completed since then.
Exterior water systems
Simcoe began by auditing the exterior water systems: irrigation, pool, while seeking target areas that might be retrofitted without requiring a complete redesign, which would likely negate potential cost savings.
Simcoe mapped the location of every building, water pipe, control valve, sprinkler-head, breakers, etc. Then they noted irrigation zones, as well as the make and model (sprinkler-heads, valves, etc.) They mapped out the type of vegetation (trees, bushes, grass, flowers, etc.) and their locations. There were over 3,000 sprinklerheads throughout the property.
The next step was to observe the irrigation system in use. Simcoe collected photos and filmed each zone as it was irrigated with specific note of:
- Overspray on buildings, residents’ cars, and sidewalks.
- Areas being irrigated where there was no need for irrigation.
- Vegetation beds not getting irrigated—Vegetation that was being irrigated unnecessarily.
Of particular importance were areas where overspray was doing damage to the building foundations; the potential damage was huge, so this was a top priority.
Now what?
The consultaing firm then developed a plan. Core components were simple:
- Eliminate problem areas
- Optimize systems for maximum efficiency
- Automize operations where possible
- Train staff, vendors, suppliers
The first priority was to eliminate those issues causing significant damage to buildings, those presented were the greatest fiscal exposure and could potentially cause thousands of dollars in damage, specifically in areas where irrigation was either spraying directly on to a building foundation or unit decking.
In those areas, Simcoe re-directed the sprinkler-head or capped them off so they would cease to do damage. All told, there were roughly 100 problem areas that were mitigated through sprinkler-head capping or re-directing irrigation.
Operating systems
The site systems were aged, and not wellsuited for the property layout. Simcoe worked within the existing irrigation map, to keep project costs efficient.
Simcoe then re-mapped the property to minimize the total number of valves and sprinkler-heads. They capped sprinklerheads that were watering mature trees, bushes and vegetation, or nothing at all. When complete, Simcoe had capped 20 percent of the community’s sprinkler-heads.
When possible, they choose to minimize any potential human error through automation. The premise: the less interaction staff had with the system, the better.
With that in mind, Simcoe added eight weather sensors throughout the property. These sensors were connected to new automatic timers that were pre-programmed for optimal irrigation. Weather sensors measure moisture levels in the air and ground. When moisture exceeds recommended levels, the sensor overrides the system and the irrigation remains off. This eliminates the irrigation turning on while it is raining.
Both the weather sensors and timers were strategically placed in locations where they could not be adjusted without the landscape manager’s assistance. Usually this meant mounting them atop buildings.
While a seemingly small detail, site tampering is a significant obstacle in mastering the highest efficiency on irrigation systems. For example, when using MP rotators, irrigation time is cut in half. Many landscapers accustomed to seven- to nine-minute watering times will increase sprinkler times on MP systems because they are unfamiliar with its process. That leads to unnecessary water expense, and even flooding.
Simcoe also helped the property owner secure rebate funds covering 85 percent of the cost of the materials for sprinklerheads, valves, weather sensors and automatic timers.
Buy-in was key to compliance
To realize full benefit on the project, Simcoe had to gain compliance from all involved. Daily operation had to be exacted for full fiscal benefit.
Simcoe met with corporate staff, onsite managers, maintenance crew and the community’s landscaping company to share:
- Strategy goals; save water and power; reduce expense, and improve performance.
- How their specific area of responsibility would be affected.
- General procedures.
- Direct benefits to the property for implementing the recommendations.
The team was excited to become part of a green property. They took ownership of the work and easily complied with execution. Tying the results of the property to their direct benefit was instrumental in gaining buy-in.
Simcoe did encounter challenges with the community’s contracted landscape company. Much of the changes, and problem areas, to which Simcoe recommended revisions were within the landscapers’ direct scope of work. The landscaper was understandably defensive.
Persuading the landscaper was a challenge, in retrospect, Simcoe wishes they would have approached the company differently.
Training, however, was successful because Simcoe’s approach was consultative and inquisitive-driven, rather than an authoritative, or domineering. Most importantly, the property owners were able to see immediate ROI to the project, according to Simcoe.
Water conservation
Water and utility-use reduction by unit was stage two of the Simcoe plan. Simcoe projected a per-unit reduction of 35 percent less water use, and 30 percent less electricity. To obtain that goal, they recommended installing the following for maximum water conservation:
- Low-flow toilets. Materials and labor: $200/per unit.
- Low-flow shower-heads, and Energy Star dishwashers (approximately $300/unit). Materials and labor under $40.
- Sink aerators in all faucets. Materials and labor under $20 per unit.
- Building-by-building grey water system, when building plumbing system needs complete retrofit.
- Rainwater harvesting system to offset the water needs of the irrigation system. With roughly 144,000 sq. ft. of roof space, approximately 90,000 gallons of water could be captured and used for the irrigation system.
To maximize utility conservation, install:
- Wall insulation in all exterior walls of each building. Closed cell foam insulation can be injected though the exterior of the building, and not disturb residents. This can cut gas bills in half for each resident.
- When replacing appliances, install Energy Star-rated appliances whenever possible. Apply for all applicable rebates and incentives to offset material cost.
- Replace all T-12 fluorescent tube kitchen and bath lighting with T-5 fluorescent tube lighting. T-5s fit into existing T-12 ballasts, so the cost is minimal while the long-term savings is great.