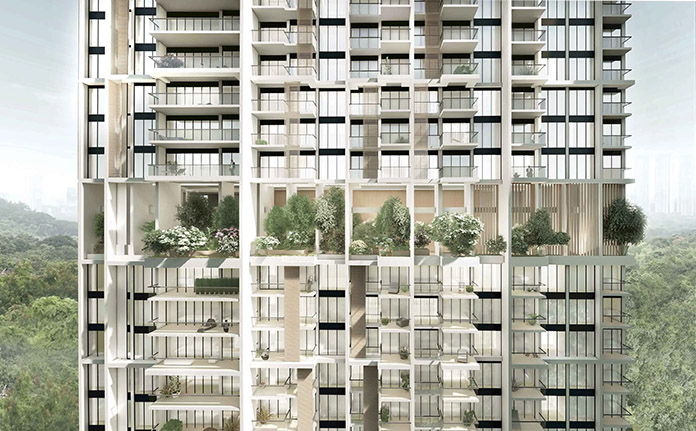
Some of the busiest apartment developers in the U.S. are still trying to use three-dimensional “modules” created in factories to reduce the cost of construction.
For more than a decade, modular construction companies promised they could save apartment developers time and money—cutting the overall cost of construction by as much as 30 percent.
Those savings in time and money can prove to be difficult to realize. For example, Forest City Ratner used modular construction create a 32-story building at 461 Dean St. in Downtown Brooklyn, N.Y. The modules were created in a factory complete with exterior walls, punch windows and even electrical outlets. The modules arrived at the construction site by truck. A crane lifted them into place.
It opened 363 apartments in 2016, after extensive construction delays.
It is still the tallest apartment tower ever made in the U.S. out of three-dimensional, factory-built modules. No other U.S. developer has attempted to match it, though taller modular apartment building have risen in the U.K. and Singapore. Forest City used conventional construction to build later phases of high-rise apartments nearby.
A decade later, a new set of developers is planning to build hundreds of new apartments with modular construction. They believe they can master the complexity of these projects and finally deliver on the promise of modular construction.
“Accelerated delivery, better quality, a higher level of sustainability, more predictability in pricing and a discount compared to stick-built construction—those are our hopes and expectations from modular technology,” said Andy Mest, managing director of development for Modern Living Solutions (MLS) at Greystar Real Estate Partners. Greystar is the busiest apartment developer in the U.S., according to the 2024 Top 50 list kept by NMHC.
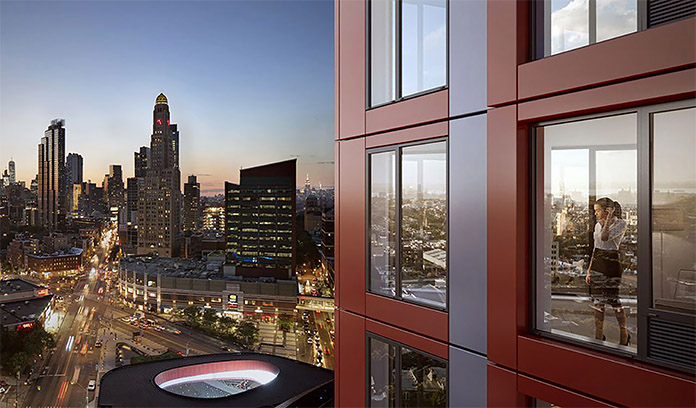
Developers keep trying modular
High interest rates and the high cost of construction materials and labor still prevent many developers from starting work on new apartment developments. The fight to bring those costs down is driving many to reconsider modular construction.
“We were very tempted—extremely tempted,” said Colin Behring, founder and CEO of the Behring Companies, based in Danville, Calif. “When construction costs and interest rates are keeping you away from getting under construction, everyone wants to find the silver bullet that will make every project pencil.”
Creating a building often requires developers to coordinate more than a dozen different teams of contractors and subcontractors. One error or delay can create a waterfall of other problems. When large parts of the building are created miles away from the construction site, the level of difficult increases.
“When you talk about modular, I twitch a little bit,” said Behring, who nevertheless continues to consider and reconsider modular construction.
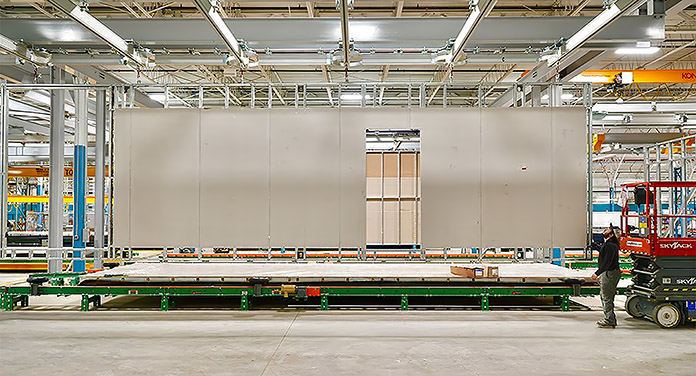
“We talk about modular every time,” said Zoltan Pali, co-founder and design principal at Studio Pali Fekete architects (SPF:a), based in Los Angeles. “It’s certainly not turned out to be something that any of my clients have wanted to do.”
Mill Creek looks for modular partners
Mill Creek Residential is now seriously considering using modular construction to build new apartments. It has already visited several modular factories in Boise, Idaho.
“We’re actually flying up in mid-August to go talk to another one,” said Eric Jensen, national director for strategic purchasing for Mill Creek Residential, working in the firm’s offices in Scottsdale, Ariz. Mill Creek is the second-largest apartment developer in the U.S., according to the 2024 Top 50 list kept by National Multifamily Housing Council (NMHC).
Mill Creek’s newest local development team, located in Salt Lake City, is looking for the opportunity to build an apartment community using modular construction. Salt Lake City is within 500 miles of Boise—that’s the furthest distance most modular companies can economically deliver their modules by truck, said Jensen.
“Our team is interested in doing a pilot modular development,” said Jensen. “They want to be the guinea pig.”
Mill Creek is fully aware of challenges developers face when they try to achieve the cost savings promised by modular construction.
Building with modules requires substantial coordination and design work much earlier than conventional construction, said Jensen. For example, architects use computer aided design to draw every aspect of the three-dimensional modules, down to the height of the electrical outlets. That may be one reason Mill Creek is interviewing potential modular companies to partner with before it even has chosen a development site.
Equity investors also contribute their money to modular construction projects earlier than convention development deals, said Jensen. This may lead developers to a new set of potential equity partners who are comfortable with the timing of modular investments.
Jensen also plans to avoid one of the deepest potential pitfalls developers face when they use a new building technology. That’s the moment in a complicated construction project when an important part of the job needs to be completed, but none of the teams have included that job in their scope of work. Jensen calls it the “scope gap.”
“Scope gaps can lead to unanticipated costs to the project—leading to budget busts,” said Jensen. For example, subcontractors hired the connect the plumbing between a line of modules might find they need to add several feet of pipe to make each connection, requiring an expensive change order.
In the years before the coronavirus pandemic—long before he joined Mill Creek—Jensen was involved in various roles in eight different developments that used three-dimensional modular components to build apartments. All eight had some version of a scope gap that had to be resolved to complete the project.
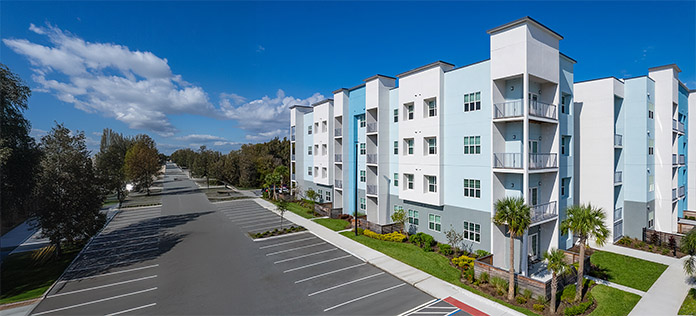
Vantem: modules, architects, equity
By the end of 2024, Trinity Development Partners plans to start construction on 264 new rental apartments at Rockledge Preserve Townhomes in Rockledge, Fla.
The new development will be built using factory-built modules created by Vantem, based in Greensboro, N.C.
The developer is confident the Rockledge Preserve Townhomes will be completed without tiresome disagreements between the creator of the modules and the contractors on site. That’s because Vantem is coordinating the general contracting and scope for the project.
“We do everything,” said Chris Anderson, founder and CEO of Vantem. “We do the architecture, the engineering, the production, the delivery and we have our general contractors that we put into the project that understand what we’re doing.”
Vantem is also contributing equity—literally taking an ownership stake in the project. That gives Trinity confidence that the developer will deliver that cost savings promised by modular construction.
“The total cost compared to traditional construction—even including just stick-built—is 20 to 30 percent less,” said Paul Shapansky, CEO and director of investment management for Trinity Development Partners, based in Boca Raton, Fla.
The two-story townhouses at Rockledge will also meet the new Zero Energy Ready Home standard created by the U.S. Dept. of Energy. A home that meets this standard is so energy efficient that a renewable energy system could offset most or all the home’s annual energy use.
Vantem’s factory-built modules can meet this standard in part because their exterior envelopeincludes a continuous layer of insulation not interrupted by wall studs that provide the structure of conventional, wood frame construction. The exterior walls are also strong enough to meet the hurricane standards of Miami-Dade County, the toughest in the country.
Trinity plans to use this energy-efficiency to qualify for PACE financing that will cover about 25 percent of the cost to develop the Rockledge Preserve Townhomes. A regular bank loan should cover another 50 percent.
The developer, Vantem and the original owner of the development site will contribute the remaining 25 percent in equity to the project.
Trinity is already planning its next modular projects.
“We have three more developments that are in our pipeline that we are working on with Vantem,” said Shapansky.
Greystar builds its own modules
Other developers that are using modular construction also plan to avoid any confusion between themselves and an outside modular company. Greystar Real Estate Partners now owns its own modular factory.
In April 2024, Greystar began pre-leasing the 312 new apartments at its Ltd. Findlay community in Coraopolis, Penn., a suburb of Pittsburgh.
“This is our first Ltd. community that is built entirely from modular construction,” said Greystar’s Mest.
Construction started on the six, plain, three-story apartment buildings at Ltd. Findlay in August 2023. The first, finished apartment will be ready for residents to move in this September—just a little more than a year later.
“We have seen great success in the accelerated delivery of the project compared to traditional stick-built construction, reducing the overall duration by 30 to 40 percent,” said Mest.
Greystar also reduced its cost of construction and achieved cost certainty much earlier in the development process compared to stick-built construction, said Mest.
The rents start at $1,598 a month for a one-bedroom apartment with 662 sq. ft. of space. The largest, most-expensive apartments rent for $2,574 a month, with three bedrooms and 1,373 sq. ft. That’s comparable to the rents at existing apartment nearby—and a considerable discount to new construction. Greystar also promises to cap rent increases for lease renewals at 3 percent or the rate of inflation, whichever is greater.
“We hope to attract essential workers that serve our community,” said Mest. “We’re providing them a new place to live with rents that are very predictable.”
Each apartment is comprised of two to four modules built at Greystar’s MLS factory in Knox, Penn., and then driven to the construction site to be stacked.
“This allows us to deliver an attainable product that is also more sustainable due to reduced construction waste,” said Mest. Greystar’s process of building Ltd. Findlay produced a tiny fraction—just 10 percent—of construction waste created by comparable convention construction.
Greystar is making modular construction work with a vertically-integrated process. In April 2023, Greystar opened its own, new, manufacturing facility with 170 full-time employees for its modular construction business. The factory is located in Knox, Penn., a rural town in western Pennsylvania that had a population of about 1,000 people in the 2020 census.
MLS is a wholly-owned subsidiary of Greystar, focused on developing housing at an “attainable” price point “at scale” according to Greystar.
“We have more than 2,000 apartments in our factory pipeline,” said Mest.
Greystar has also considered using modular construction in its other apartment development projects including high-rise buildings. However, the high-rise residential market is a very small percentage of the US housing market. “It is a bespoke product that does not allow for us to scale our business in a meaningful way,” said Mest.
In contrast, roughly 95 percent of the rental apartments in the U.S. are in midrise and low rise buildings.
“For the interim we are laser focused on essential housing and serving the missing middle,” said Mest. “This is a very large opportunity that is virtually untapped at scale.”
Panelized construction becomes conventional
Other building technologies that seemed cutting edge a decade or so ago are now almost standard for many developers—such as panelized construction.
Many high-rise developers now depend on panelized construction, especially for sections of ready-made exterior wall. “That is really the only way to make those things work,” said Pali. “Certainly on taller buildings, you are using skin systems that are absolutely panelized.”
Leading developers have made panelized construction work for low-rise and mid-rise buildings.
“We’ve had a generally positive experience with panelized construction,” said Andrew Beach, senior vice president of community technology and innovation for Mill Creek Residential, working in the firm’s offices in Denver, Colo. “Panelized construction helps improve the construction schedule, reduce waste and reduce labor on site.” Mill Creek regularly uses panelized construction and hybrid models on apartment projects in Massachusetts, for example, new project in Marshfield will utilize a hybrid method, said Beach.
However panelized construction doesn’t make every project more efficient.
“Our firm has explored the potential of panels and modular construction for many years,” said Marc Padgett, president of Summit Contracting Group, a leading multifamily general contractor, based in Jacksonville, Fla. “The theory is great, but when breaking down a “stick-build” versus a modular build, there is no cost savings for us in our Southeastern markets.”
For many projects, it is a needless step to deliver lumber to a factory, nail it together to create much bulkier wall panels and deliver those panels to the exact part of the construction site where they are needed, according to Padgett. “It literally quadruples your trucking costs,” said Padgett.
Efficient design saves money
Other developers are designing apartments to be more cost-effective. Behring’s new building at 1900 Broadway includes 10 four-bedroom apartments designed for roommates.
“The kitchen is astronomically more expensive to build than floor space,” said Behring. “The cost to build those four-bedroom units per sq. ft. versus a studio is probably 35 to 50 percent less.”
These four-bedroom apartments have rented quickly to sets of two or four adults who plan to become roommates—such as younger technology workers—or college students attending the University of California Berkeley, just nine minutes away. The rents start are about $6,800 a month, or $1,700 per bedroom.
In comparison, a two-bedroom unit in any Class A tower in San Francisco or Oakland would cost between $5,000 and $6,000. “We can offer four bedrooms for about the same price,” said Behring.